Product Codes:
ER2223
Electrolube’s high performance ER2223 resin proved successful in the requirement for a material to electrically insulate a stator coil for an automotive application. Find out more on how this highly chemical resistant potting compound, formulated to meet the harsh operating conditions of under-hood applications was proven to be the most effective solution.
Make it with our expertise.
Superb research facilities, expert people and leading technologies allows us to provide solutions tailored to your specific industry challenges.
With our expansive product range of formulated chemical products, we supply leading manufacturers of electronic, industrial and domestic devices for a variety of industries, thus offering the ‘complete solution’ at all levels of production.
Our unrivalled, very personal customer service also extends to every corner of the world. You can rely on our fully trained staff to be knowledgeable and up to speed with the latest technological developments. Having a named single point of contact helps ensure we work closely with our customers, solving problems in the most efficient way possible.
See how Electrolube has helped solve problems for other businesses in your industry.
- Automotive
- Military
- Aerospace
- Transport
- Marine
- Telecommunications
- Medical
- Consumer electronics
- Industrial electronics
- Transport
- Utilities
- Service, repair and maintenance
- LED
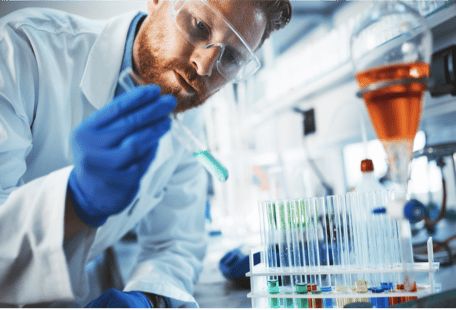
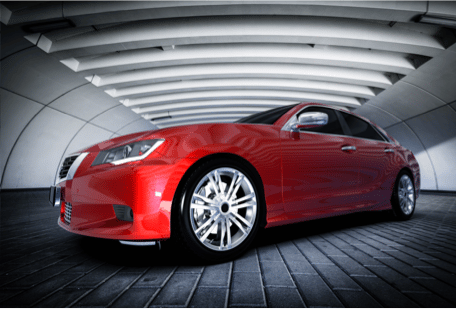
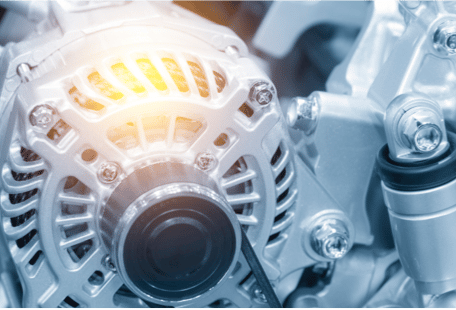
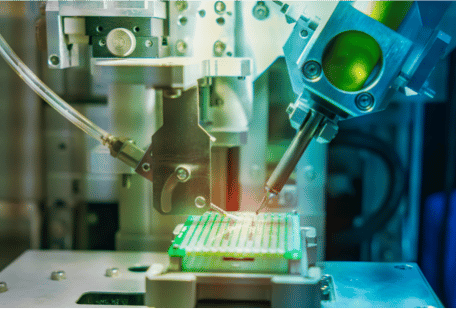
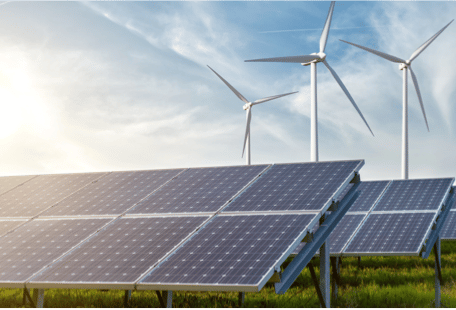
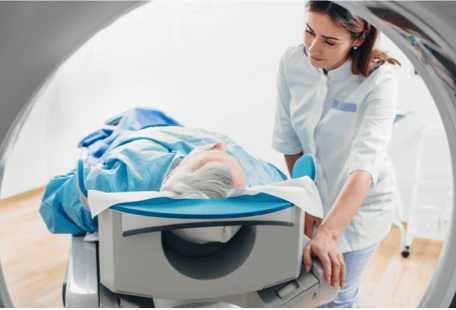
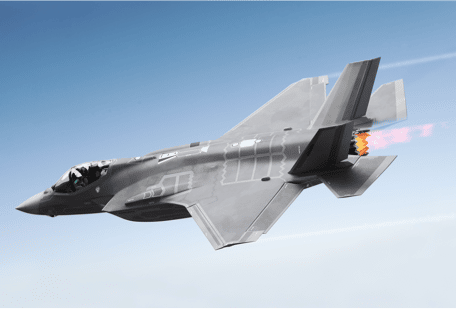
Make it our problem.
With our expansive product range of formulated chemical products, we supply leading manufacturers of electronic, industrial and domestic devices for a variety of industries, thus offering the ‘complete solution’ at all levels of production.
If our range does not quite meet your requirements, our technical support or research and development teams will work with you to solve your chemical problem and supply the perfect solution.